Classification Models for Hazard Prediction in Mining
- Rob Raheb
- Mar 4
- 3 min read
Updated: Mar 11

In the mining industry, safety is paramount. Harsh working conditions, heavy machinery, and dynamic underground environments combine to create a wide range of potential hazards. Predicting these risks before they escalate can literally save lives—and this is where classification models shine.
Bear Cognition harnessed the power of classification to build a predictive system that proactively flags dangerous conditions. This post explores the core principles of classification, how these models were tailored for the mining sector, and the resulting impact on safety and operations.
The AI Capability: Classification
Classification models use historical data to identify patterns and assign labels—such as “safe” or “unsafe.” Techniques like decision trees and random forests are particularly effective, as they analyze multiple variables simultaneously and identify the combinations most associated with risk. Think of it as a digital risk assessor.
Why Classification Works for Mining:
Multiple Data Sources: Mining operations generate diverse data (e.g., equipment sensor data, worker movements, environmental conditions). Classification models can handle and integrate these varied inputs effectively.
High-Risk Indicators: Techniques like decision trees and random forests excel at identifying strong predictors of accidents, such as equipment malfunction rates or elevated gas levels.
Real-Time Potential: Once trained, these models can run continuously, evaluating new incoming data to provide immediate alerts.
The Process

The system was trained using sensor data from machinery, worker locations, and environmental conditions. Steps included:
Data Collection: Gathered historical incident reports, sensor data from machinery, worker location tracking, and environmental measurements (like air quality and temperature).
Data Labeling: Used historical records and expert input to categorize past incidents as “hazardous” or “non-hazardous.” This labeling step laid the groundwork for model training by defining what constitutes a hazard.
Feature Engineering: Identified key variables (features) most relevant to hazard prediction, such as:
Proximity to active machinery
Time of day or shift pattern
Equipment health indicators (e.g., vibration levels, temperature spikes)
Environmental conditions (e.g., humidity, gas levels)
Additionally, new derived features were created to capture nuanced aspects—for example, “distance to nearest exit” or “maintenance status age” (time since last maintenance).
Model Training & Validation: Employed algorithms like Random Forest, Decision Trees, and Logistic Regression. Data was split into training and testing sets to ensure generalizability and avoid overfitting. Multiple rounds of cross-validation further refined accuracy and performance.
Deployment & Real-Time Monitoring: Integrated the finalized model with live data streams from sensors and operational dashboards. Automated alerts were set up to trigger whenever the model detected a high-risk scenario, ensuring timely intervention.
Outcome & Capabilities
Reduced Safety Incidents
By detecting risky situations in advance, the classification model played a pivotal role in minimizing accidents. For instance, an abnormal vibration reading combined with a worker being in close proximity would trigger an immediate alert.
Empowered Teams
Armed with real-time, predictive insights, the operational staff could swiftly intervene. Whether it meant scheduling urgent machinery maintenance or redirecting workers to safer zones, the model’s alerts helped teams act before issues escalated.
Scalability
Because classification algorithms can be re-trained with new data, the system evolves alongside the operation. As mining sites adopt new machinery or encounter different environmental conditions, the model seamlessly integrates these updates for continuous improvement.
Conclusion
Classification models are more than just another AI tool; they are safety multipliers in high-risk environments like mining. By focusing on the right data and tuning algorithms to spot hidden danger signals, Bear Cognition’s classification system delivers timely, actionable insights. The result is a safer workspace, reduced downtime, and a resilient operation that can adapt as conditions change.
Interested in learning more? Contact Bear Cognition today for a deeper dive into how predictive classification can enhance safety protocols in industrial settings.
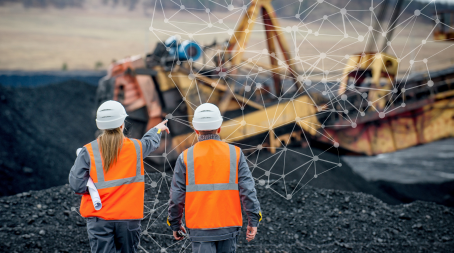